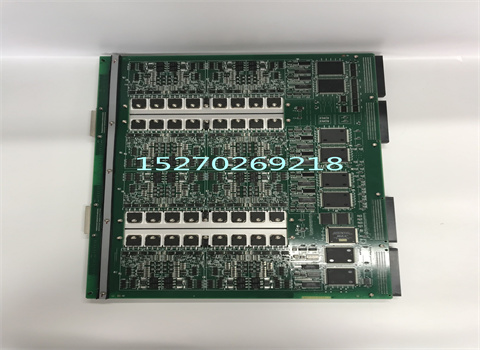
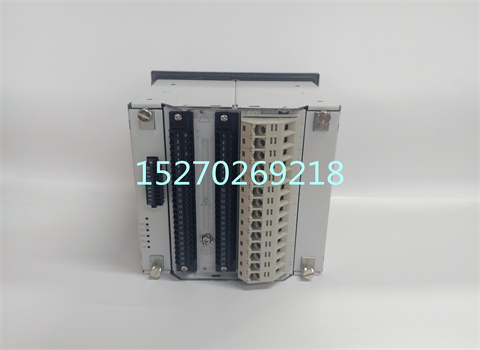
主营产品,备件供应,充足库存
Foxboro(福克斯波罗):I/A Series系统,FBM全系列(现场输入/输出模块)
顺序控制、梯形逻辑控制、事故追忆处理、数模转换、输入/输出信号处理、
数据通信及处理等。
Westinghouse(西屋):1C31系列DCS系统、CPU、OVATION系统、WDPF系统、
WEStation系统备件。
Triconex(英维思):冗余容错控制系统、基于三重模件冗余(TMR)结构的现代化的容错控制器。
EMERSON(艾默生):模块、卡件、驱动器等各类备件。
XYCOM:XVME系列
Bently(本特利):3500/3300系统。
Rockwell(罗克韦尔):ICS系统。
ABB:PM全系列DCS系统、IGCT高压变频器系列、工业机器人备件DSQC系列、INFI 90等。
Bailey(贝利):BRC系列DCS系统等。
Allen-Bradley:1756、1785、1771、1746全系列系统等。
Yokogawa(横河):CP系列等。
Honeywell(霍尼韦尔):TK/TC/CC系统等。
Reliance(瑞恩):57C系列等。
Schneider(施耐德):140系列处理器、控制卡、电源模块等。
Modicon(莫迪康):AS系列PLC系统备件。
Siemens(西门子):6ES5/6ES7414/6ES7415/6ES7416系列PLC系统备件、
Siemens MOORE,Siemens Simatic C1,Siemens数控系统等。
Motorola(摩托罗拉):MVME 162、MVME 167、MVME1772、MVME177等系列。
XYCOM:I/O、VME板和处理器等。
GE(通用电气):IC698/IC697全系列PLC系统、模块、卡件、驱动器等各类备件。
Yaskawa(安川):伺服控制器、伺服马达、伺服驱动器。
Bosch Rexroth(博世力士乐):Indramat,I/O模块,PLC控制器,驱动模块等。
Woodward(伍德沃德):SPC阀位控制器、PEAK150数字控制器。
The parameter setting of PID is the core content of the control system design of injection molding machine. It is to determine the pressure, speed, temperature PID control proportion coefficient, integration time and differential time according to the characteristics of injection molding process. There are many methods to set PID control parameters, which are summarized in two categories: one is theoretical calculation and setting. It is mainly based on the mathematical model of the action system of the injection molding machine, and the control parameters are determined by theoretical calculation. The calculation data obtained by this method may not be directly used, but also must be adjusted and modified by the actual action of injection molding machine. The second is the setting method of the action process of the injection molding machine. It mainly relies on the experience of the injection molding machine action control, and directly adjusts the pressure, speed and temperature when the injection molding machine is running. The method is simple and easy to master, and is widely used in the commissioning of the injection molding machine. The engineering setting methods of PID control parameters are mainly critical proportion method, reaction curve method and attenuation method. The three methods have their own characteristics, and their common point is to pass the test, and then adjust the PID parameters according to the experience of injection molding machine debugging. However, no matter which method is adopted, the PID parameters need to be adjusted and perfected in practice. During the field setting of injection molding, we should keep PID parameters in the order of proportion first, then integration and final differentiation. While observing the trend curve of field process value PV, slowly change PID parameters and make repeated trial until the control quality meets the requirements. In the setting of injection molding machine pressure, speed and temperature, we usually turn off integral term and differential term first, i.e. ti is set to infinity and TD is set to zero, so that it can be adjusted as pure proportion. The initial scale is set according to the empirical data, and the proportion is controlled slowly according to the PV curve, so that the system can achieve the PV curve with 4:1 attenuation oscillation, and then add the integral function. Before the integral action, the proportion should be increased to about 1.2 times of the original. The integration time ti is adjusted from large to small until the system obtains the PV curve of 4:1 attenuation oscillation again. If differential action is needed, the differential time is calculated according to td= (1/3-1/4) Ti. Then the scale can be adjusted to the original value or smaller, and then the differential time can be adjusted from small to large until the PV curve reaches satisfaction. One thing to note is that in the process of trial, if Ti and TD are to be changed, the ratio should be kept unchanged. Before finding the best setting parameters, we should analyze the trend of PV value curve, judge the change of disturbance, and then make a trial slowly. If the optimal setting parameters or parameters cannot be found after many times, and the injection molding process must be more accurate, the effectiveness of single loop PID control should be considered, and more complex PID control should be selected. It is worth noting: after the PID optimal setting parameters are determined, it can not be explained that it is always the best. When the fundamental change occurs due to external disturbance, for example, the pressure proportional valve is adjusted and cleaned, and the heating ring is replaced. In fact, if the temperature is to be precisely adjusted, different products, different back pressure and thermal inertia are different, all of them need to be adjusted! We must readjust the optimal parameters according to the needs, and it is also an important link to ensure the effectiveness of PID control.