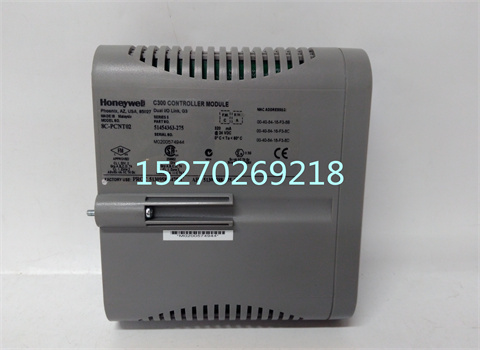
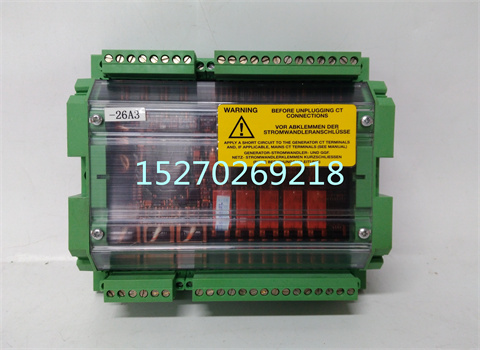
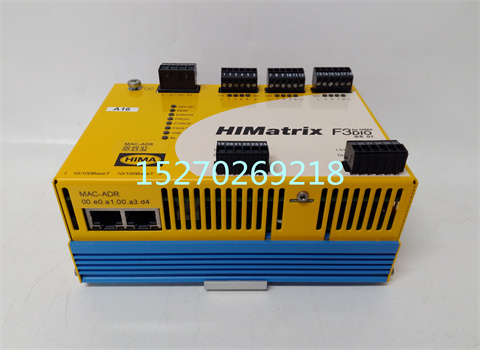
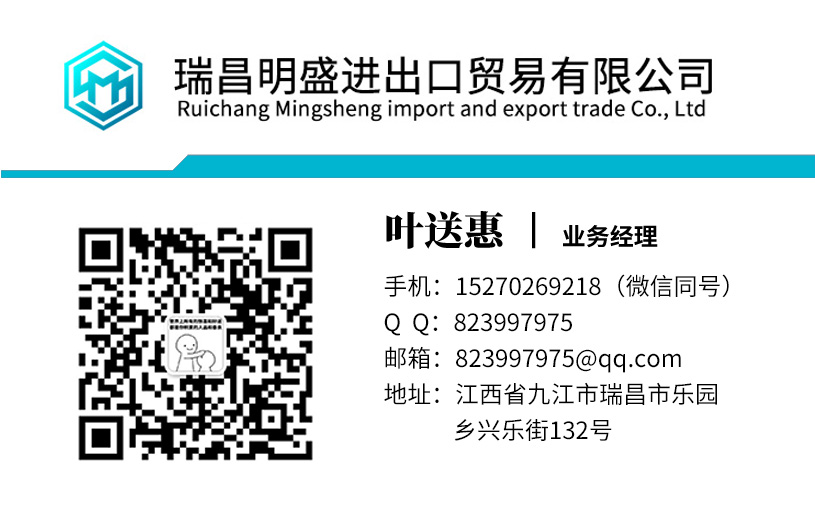
在线咨询买家必读:
一、店铺所有价格均不是实价,如需了解产品价格,请联系在线客服。
二、现货付款当日发货;期货从付款日起开始计算时间,货期不含国内外节假日。
三、买家通过快递或物流签收货物后,若有异议,请在收到货物当天内提出。
1、下单前,买家需向卖家确认价格和货期;若买家单方面下单,则订单视为无效;
2、下单后,买家不得更改产品品牌,规格型号以及数量、单价等,因买家提供产品规格型号错误而造成错误订货的,卖家不负责更换货品、退货、退款等,也不承担因此造成的损失;
3、下单后,若无质量问题,不接受无理由退/换货、退款;
4、因此产品生产厂家停产、升级无3C、涨价、受限制造成无法订货,则订单取消,卖家不承担任何相关法律责任;
5、因自然天气、运输货运、政法政治原因等非卖方所能控制之客观因素导致货期延误,卖家不承担任何相关法律责任,由买卖双方协商订单是否依旧生效。
请各位买家知悉相关条款,如有异议,请咨询解决相关疑问!
The parameter setting of PID is the core content of the control system design of injection molding machine. It is to determine the pressure, speed, temperature PID control proportion coefficient, integration time and differential time according to the characteristics of injection molding process. There are many methods to set PID control parameters, which are summarized in two categories: one is theoretical calculation and setting. It is mainly based on the mathematical model of the action system of the injection molding machine, and the control parameters are determined by theoretical calculation. The calculation data obtained by this method may not be directly used, but also must be adjusted and modified by the actual action of injection molding machine. The second is the setting method of the action process of the injection molding machine. It mainly relies on the experience of the injection molding machine action control, and directly adjusts the pressure, speed and temperature when the injection molding machine is running. The method is simple and easy to master, and is widely used in the commissioning of the injection molding machine. The engineering setting methods of PID control parameters are mainly critical proportion method, reaction curve method and attenuation method. The three methods have their own characteristics, and their common point is to pass the test, and then adjust the PID parameters according to the experience of injection molding machine debugging. However, no matter which method is adopted, the PID parameters need to be adjusted and perfected in practice. During the field setting of injection molding, we should keep PID parameters in the order of proportion first, then integration and final differentiation. While observing the trend curve of field process value PV, slowly change PID parameters and make repeated trial until the control quality meets the requirements. In the setting of injection molding machine pressure, speed and temperature, we usually turn off integral term and differential term first, i.e. ti is set to infinity and TD is set to zero, so that it can be adjusted as pure proportion. The initial scale is set according to the empirical data, and the proportion is controlled slowly according to the PV curve, so that the system can achieve the PV curve with 4:1 attenuation oscillation, and then add the integral function. Before the integral action, the proportion should be increased to about 1.2 times of the original. The integration time ti is adjusted from large to small until the system obtains the PV curve of 4:1 attenuation oscillation again. If differential action is needed, the differential time is calculated according to td= (1/3-1/4) Ti. Then the scale can be adjusted to the original value or smaller, and then the differential time can be adjusted from small to large until the PV curve reaches satisfaction. One thing to note is that in the process of trial, if Ti and TD are to be changed, the ratio should be kept unchanged. Before finding the best setting parameters, we should analyze the trend of PV value curve, judge the change of disturbance, and then make a trial slowly. If the optimal setting parameters or parameters cannot be found after many times, and the injection molding process must be more accurate, the effectiveness of single loop PID control should be considered, and more complex PID control should be selected. It is worth noting: after the PID optimal setting parameters are determined, it can not be explained that it is always the best. When the fundamental change occurs due to external disturbance, for example, the pressure proportional valve is adjusted and cleaned, and the heating ring is replaced. In fact, if the temperature is to be precisely adjusted, different products, different back pressure and thermal inertia are different, all of them need to be adjusted! We must readjust the optimal parameters according to the needs, and it is also an important link to ensure the effectiveness of PID control. Of course, in the actual injection molding production only a period of time to carry out a verification can!